Burning The Toast
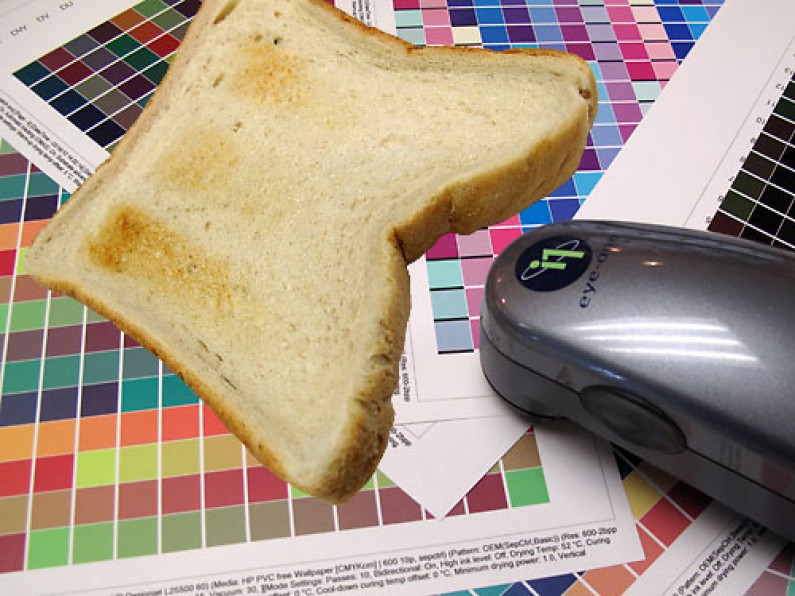
Matching colours correctly; it is a process that happens behind the scenes. You might not realise how important it is and why we take it so seriously. A number of years ago I read an article which is a great way to describe why colour management so important. It's all about making toast!
Here is my take on burning toast...
You throw a piece of bread into your toaster (T1) on setting 4, eventually it pops up a shade of brown. You grab your bag of bread and head next door. You then do the exact same process on your neighbours toaster (T2) and no surprise, the two pieces of toast look different. Assuming we want them the same, how can we get them to match? We have two options.
Option 1, We dial up and pop out a piece of toast on each setting 1-10 on T2, then line them up as a chart. When we need to match a 'toast colour' from T1 on T2, we visually compare a T1 toast colour to our toast chart and turn the dial on T2 to the setting that is the best match.
Option 2, We toast bread on each setting 1-10 on T2, but this time we measure them with a special toast colour reading device and save the values into a software program (which now controls the toaster). The software analyses the values and adjusts the electricity flow so T2 can now toast in nice even toast colour steps from 1-10. We continue to let the software toast and measure hundreds of pieces of bread so we get even more shades of brown. The same thing is also done on T1, so the software now knows every shade for both toasters. The software compares every T1 toast colour requested to it's measured toast colour library and gives the T2 setting to use for a best match, it even changes T2's setting itself.
Which option?
Option 1 sounds like an easy option. But what happens if the heating elements get tired and T2 changes over time, the toast chart is still on the wall with the original colours, but the toast now popping up isn't the same original colour. Did it get spotted by the toast operator? Probably not. It is cross your fingers and hope for the best. No, it's not a good option.
Using option 2, we have everything contained in a software program, even better, we can regularly re-toast levels 1-10 so the software re-calibrates the electricity supply so the hundreds of readings we took are still accurate. We still know the software will correctly match the toast shades, even if the toaster elements have gotten tired.
Now visualise that Toaster 1 is your file (colour working space), and Toaster 2 is our printer's colour working space.
This is colour management. It is a precise method of measurement, or without it, a manual hit and miss situation. We do take colour management seriously… and you benefit from it, every print.
Putting all this together in colour printing terms.
You provide files with an icc profile attached/embedded (Working Colour Space). We calibrate our printers/media and create a colour space (icc profile) of all achievable colours on that device. Our software compares your file to our printer and then converts the CMYK formulations to match, even RGB files. When the file is processed, a blue colour in your file of Cyan 50%, might need changing to Cyan 30% Magenta 3% to create the exact same colour with our printer. If were to re-run the job a year on, because we re-calibrate our printers regularly, any colour shifts in the printer will be accounted for and the output will still be correct. On the other hand, if we just ignored colour management and used your file setting of Cyan 50% then the colour will be too dark and wrong every time. A year later it might be different again as the printers ink densities shift.
QUALITY - RELIABILITY - CONSISTENCY
Happy Toasting!!!